Steel silo is a kind of advanced storage equipment used for storing powdery, granular materials and liquids, in common parlance, any silo made of steel plate is called steel silo. Steel silo is mainly used to store cement, fly ash, slag powder, clinker, grain and other materials, but also can be applied to the storage of sulfuric acid and other liquids.
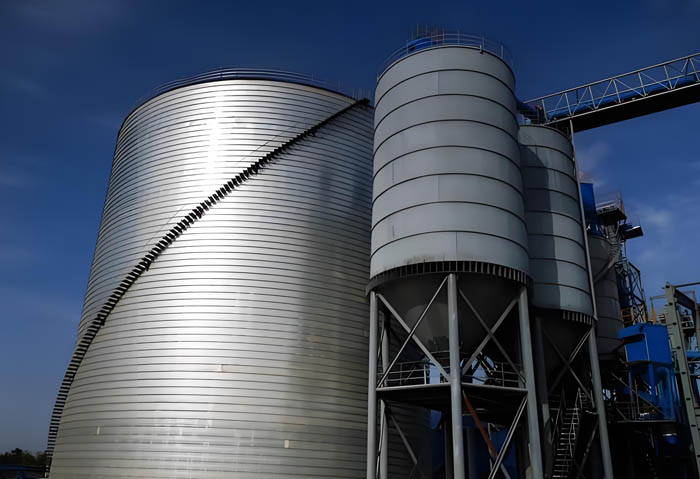
Steel silo is how to categorized
According to its construction method and process characteristics, steel silo can be roughly divided into three types: bolted steel silo, spiral steel silo, welded steel silo, each type has its unique advantages and applicable scenes.
1.Bolted steel silo
Bolted steel silo is a kind of prefabricated assembly storage structure, through the factory pre-drilling of steel plate precision, and then in the construction site using high-strength bolts to these prefabricated parts are closely connected together. This construction method gives the bolted steel silo the following characteristics:
Economy and Flexibility: Due to standardized production, the cost is relatively low, and it is easy to adjust the size of the silo according to the actual demand, making the construction cost more economical. At the same time, its removability allows the warehouse to be relocated or reconfigured as needed, improving resource utilization.
Rapid installation: The on-site assembly process is simple and quick, reducing the construction cycle and the dependence on the professional skills of the installers, which is suitable for rapid deployment of storage needs.
Airtightness limitation: Although the high-strength bolts ensure the stability of the structure, but compared with the welded or spiral bite structure, its airtightness is poor, and is not suitable for storing powdery or perishable materials that require high sealing.
2.Spiral steel silo
Spiral steel silo utilizes the “cold roll bending” technology to form a spiral structure by continuously cooling and laminating the steel silo, which is especially suitable for thin sheet materials. Features include:
Excellent sealing: The spiral bite design ensures the tightness of the silo body, which is very suitable for storing powdery materials such as cement, fly ash, etc., and effectively prevents material leakage and moisture.
Strong seismic performance: the continuous cold-formed bottom plate enhances the overall stability and seismic capacity of the structure, which has been verified by many strong seismic tests to be safe, reliable and have a long service life.
High technical threshold: the construction process requires strict requirements on the professional skills of the equipment operators and the quality of the reel materials, which limits its wide application.
Higher cost: Due to the complexity of material selection and process, the construction cost of spiral steel silo is usually higher than bolted type.
3.Welded steel silo
Welded steel silo is a large-scale storage equipment constructed through steel plate welding technology, which represents the independent research and development achievements of China’s steel silo technology. Its main features include:
Large-capacity storage: the capacity of a single silo can reach 10,000 to 100,000 tons, which is easy to be combined into a larger storage group to meet large-scale storage needs.
Structural robustness: Welded connections provide high strength and stability, capable of withstanding large loads and external environmental pressures.
Maintenance Requirements: Welded structures are generally more durable, despite the longer construction period and higher weight, but require regular anti-corrosion treatments to extend service life, typically every 3-5 years.
Widely applicable: suitable for the storage of a variety of materials, including grain, chemical raw materials, etc., but considering its weight and construction complexity, it is more suitable for long-term use in fixed locations.
Extend the service life of steel silo methods
1.Regularly check the appearance of the steel silo, including any obvious damage, corrosion, deformation and so on. Observe whether there is any leakage, cracks and other problems in the silo, and repair them in time.
2.Regularly clean the inside of the steel silo, including cleaning the accumulated fly ash, dust, etc.. Use appropriate tools and equipment for cleaning to maintain the cleanliness of the silo.
3.After unloading the empty silo, check the sealing of the silo, as well as the door frame and adjacent side panels for deformation or cracks. If abnormalities are found, appropriate measures should be taken in a timely manner. Also check the articulation part of the cone bucket has no abnormality and deal with it.
4.Check the safety equipment in the steel silo, such as fire extinguishing equipment, safety valves, etc., to ensure that the safety equipment is in good condition and effective, in order to cope with unexpected situations.
5.Establish detailed maintenance and inspection records, including the date of inspection, inspectors, inspection content, etc.. Record the maintenance and repair work for subsequent reference.
AGC Steel Silo Engineering Co., Ltd is a leading and well-known steel silo manufacturer in China, we have construction projects in more than 30 countries and regions such as Russia, Tanzania, Ethiopia, Congo, Indonesia, Malaysia and so on, with more than 500 sets of steel silos, and our quality and reputation are highly recognized by users all over the world. For more information about silo engineering and storage silo solutions, please contact us or leave your request.
Leave a Reply